عملیات استاندارد چیست ؟
استاندارد سازی چگونه به سرپرست کمک می کند که به اهداف کمی و کیفی تیم کاری خود دست پیدا کند؟
شاید برخورد داشته اید که اپراتورهای مختلف یک فرآیند خاص را با روش های مختلف و در زمانهای متفاوت انجام می دهند.
ممکن است این سوال پیش آید که نحوه و زمان انجام فرآیند برای مشتری اهمیتی نداشته و فقط کیفیت محصول مد نظر برای مصرف کننده و یا دریافت کننده خدمات مهم باشد.
پاسخ این شبهه این است که نحوه متفاوت انجام فرآیند از این رو مهم است که همیشه بهترین روش انجام کاری وجود دارد که نشانگر مهارت بالای اپراتور و تضمین کننده کیفیت محصول و حداقل زمان صرف شده جهت انجام آن فرآیند می باشد و هرگونه تغییر در انجام این روش ممکن است در کیفیت و قیمت تمام شده محصول یا خدمت تاثیر گذار باشد.
روش های متعدد و مختلف انجام کار نیز ممکن است علاوه بر صدمه زدن به قطعات، باعث بروز ایرادات کیفی هرچند جزیی می گردد که منجر به دوباره کاری و صرف زمان می گردد.
از طرفی افزایش زمان انجام فرآیند در تیراژتولید بالای محصول بصورت تصاعدی روی زمان انجام سایر فرآیند ها نیز تاثیر داشته (ایجاد گلوگاه) و این موضوع باعث افزایش قیمت تمام شده محصول می گردد که یا حاشیه سود تولید کننده را کاهش میدهد یا باعث بالا رفتن قیمت محصول می گردد که مستقیما روی مشتری تاثیر می گذارد.
استاندارد سازی، راه کار رفع این معضل می باشد. استاندارد سازی تدوین عملیات استاندارد برای تک تک فرایند های جاری تولید یا ارائه خدمات می باشد.
عملیات استاندارد بر گرفته شده از نحوه انجام فرآیند یا خدمت، توسط ماهرترین فرد مجموعه می باشد.
تعریف عملیات استاندارد:
بهترین روش انجام کار در حال حاضر که در بر گیرنده بهترین کیفیت محصول، کمترین زمان انجام و تضمین کننده کمترین خستگی اپراتور و خطرات احتمالی باشد.
استاندارد سازی با ایزو یا سایر استاندارد های جاری متفاوت است ولی استقرار استانداردسازی کمک زیادی به بالا بردن فرهنگ سازمان و ایجاد زمینه جاری سازی استانداردهای بین المللی خواهد کرد و اصل و اساس فرهنگ استاندارد است و شاهد خوبی برای ممیزین استقرار استاندارد های مختلف مانند ایزو، جایزه تعالی سازمانی و …… خواهد بود.
چگونه استاندارد سازی کنیم؟
همانگونه که در بالا مطرح شد ملاک یک عملیات استاندارد، نحوه و روش انجام کار توسط ماهرترین فرد مجموعه می باشد که باید با دقت و ذکر جزئیات ثبت گردد.
نکته بسیار مهم این است که شاید راه های بهتری جهت انجام یک فرایند وجود داشته باشد. مثلا استفاده از ابزاری خاص که فعلا خریداری نشده و موجود نیست. این امر نباید ثبت عملیات استاندارد را به تاخیر بیاندازد تا آن تجهیز یا ابزار تهیه گردد زیرا در این صورت ممکن است کار متوقف شده و دیگر انگیزه و اصراری جهت انجام استاندارد سازی نباشد. از این رو توجه شما را به عبارت “در حال حاضر” در تعریف عملیات استاندارد جلب می کنم.
این یعنی منتظر بهبود های بلند مدت نباشید هر آنچه هست ثبت کنید و در اولین فرصت در مورد بهبودهای روش انجام کار فکر کنید و تصمیم بگیرید و در برگه عملیات استاندارد تغییر دهید.
از دیگر مزایای استقرار استاندارد سازی، جلوگیری از فراموشی بهبود های ایجاد شده و به نوعی برگشت به عقب و الزام تمامی پرسنل به اجرای بهبود می باشد
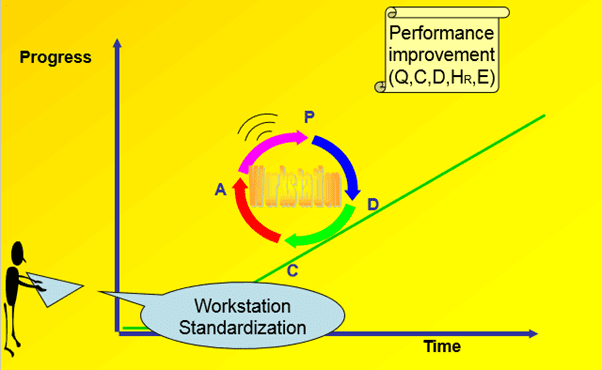
حال که صحبت به اینجا رسید بد نیست اشاره ای کنیم به چرخه بهبود مستمر یا چرخه دمینگ یا چرخه PDCA، که افرادی که با مفاهیم تولید و کیفیت سر و کار دارند با آن آشنایی دارند .
قبل از بکار گیری چرخه PDCA بایستی چرخه SDCA ایجاد شود. S در این چرخه به معنی استاندارد سازی است و گام قبل از چرخه بهبود مستمر، چرخه استاندارد سازی می باشد چرا که “هر آنچه که استاندارد نشده باشد قابل بهبود نیست.”
ابتدا باید بدانیم که چه می کنیم سپس بهبود دهیم. دقیقا مانند روش های حل مسئله که یکی از مراحل اولیه آن “درک وضعیت جاری” می باشد.
به عنوان مثال در متدولوژی شش سیگما به روش DMAIC حرف M مخفف کلمه Measure به معنای اندازه گیری شاخص های فعلی می باشد و استاندارد سازی در همان اوایل اجرای پروژه، به کاهش پراکندگی ها در اطلاعات جمع آوری شده کمک میکند.
خلاصه اینکه استاندارد سازی سنگ زیر بنای تمام سیستم های تولید و کیفیت است. اگر تمامی پرسنل در تمامی روزها، تمامی شیفت های کاری، تمامی شعب به طور یکسان کار کنند اگر خطایی هم وجود داشته باشد به راحتی قابل ردیابی، شناسایی و برطرف کردن می باشد و اگر تنوع روش های کاری را شاهد باشیم، مشکل در یک مقطع زمانی هست و تا بیاید بررسی صورت بگیرد، برطرف میشود و بار دیگر بصورت غافلگیر کننده بروز می کند.
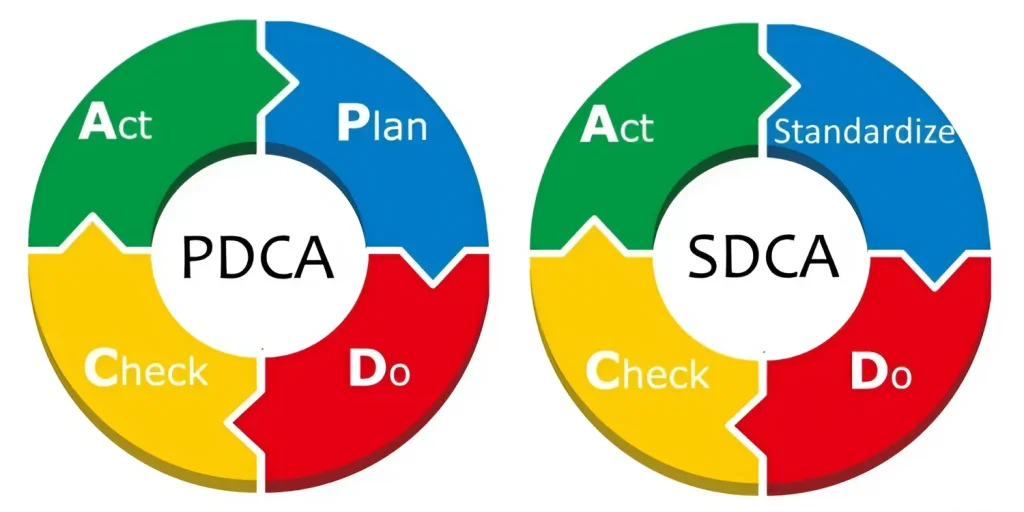
چگونه استاندارد سازی کنیم ؟
کار با تهیه و تدوین برگه عملیات استاندارد آغاز میشود، برگه عملیات استاندارد به SOS معروف است.
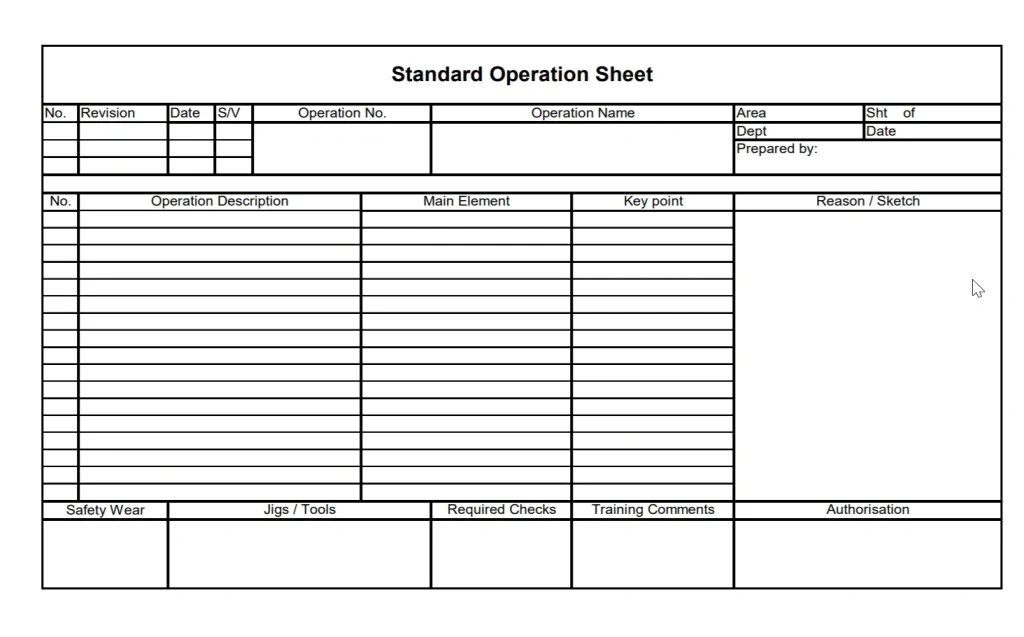
علاوه بر نیروی کار ماهر در هر پست کاری به عنوان مرجع جهت تدوین برگه عملیات استاندارد، مدارک فنی و مهندسی نیز که توسط طراح محصول تهیه و تدوین شده است نیز از مراجع بسیار مهم جهت تدوین SOS میباشد که به POS برگه فرایند عملیات معروف است.
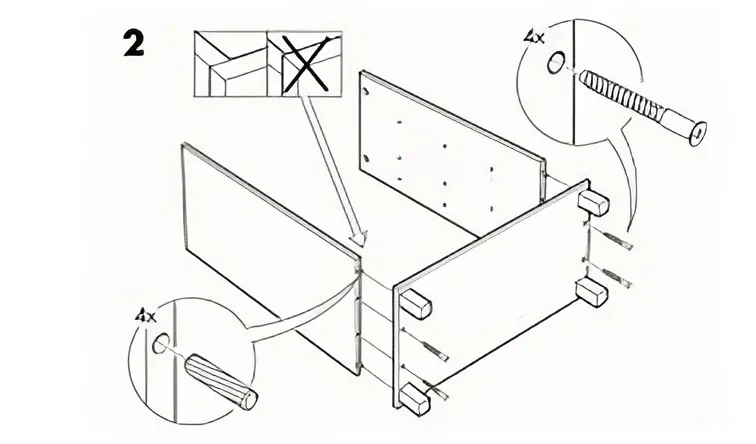
با توجه به نوع عملیاتی که دردستور کار استاندارد سازی هست فرمت SOS متفاوت می باشد.
انواع عملیات :
عملیات با سایکل تایم کم ( کمتر از 5 دقیقه )
عملیات با سایکل تایم بالا ( بیشتر از 5 دقیقه )
عملیات ترکیبی اپراتور با ماشین الات
عملیات کنترل کیفیت
عملیات تعمیراتی
نوع عملیات |
SOS پیشنهادی |
عملیات با سایکل تایم کم (کمتر از 5 دقیقه) |
SOS آنالیز |
عملیات با سایکل تایم بالا (بیشتر از 5 دقیقه) |
SOS فرآیند |
عملیات ترکیبی اپراتور با ماشین الات |
SOS انسان – ماشین |
عملیات کنترل کیفیت |
SOS کیفیت |
عملیات تعمیراتی |
SOS جریان عملیات |
هر SOS دارای فرمت مختص خود می باشد که در آن متناسب با نوع عملیات، ستون ها و بخش های طراحی شده است که به راحتی بتوان عملیات مورد نظر را شرح داد.
این برگه توسط سرپرست پس از گذراندن دوره SOS نویسی و کسب امتیاز لازم به تایید مربی استاندارد سازی، تهیه و تدوین می گردد و در صورت نیاز به تغییر، به علت تغییرات شرایط کاری یا محصول و یا بهبود، بازنگری می گردد.
در نوشتار بعدی به جزئیات برگه های SOS و نحوه تکمیل و ادبیات شرح فعالیت می پردازیم.
منابع :
- معجزه چابکی، محمد نجار کریمی،سال انتشار 1400 ، انتشارات ارشدان
- سرپرست جامع،محمد نجار کریمی،سال انتشار 1400 ، انتشارات ارشدان
- راه تولید نیسان،ترجمه مهدی گیلی، پرویز فرضی، انتشارات راه ابریشم1390
- سایت مدیر ناب Modirnab.com
- آموزش ها و تجربیات اجرایی استقرار سیستم های تولید وکیفیت شرکت رنو SPR،شرکت ایران خودرو معاونت تندر1385
همچنین شما میتوانید جهت مطالعه دیگر مقالات تخصصی کلینیک مدیر ناب، از فهرست زیر استفاده نمایید یا به صفحه مقالات ما مراجعه فرمایید!
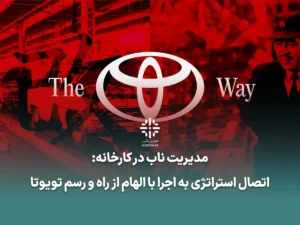
مدیریت ناب در کارخانه: اتصال استراتژی به اجرا با الهام از راه و رسم تویوتا
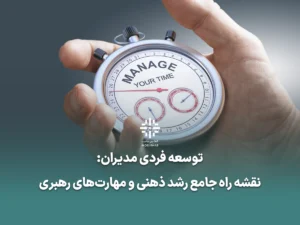
توسعه فردی مدیران: نقشه راه جامع رشد ذهنی و مهارتهای رهبری در سال 1404
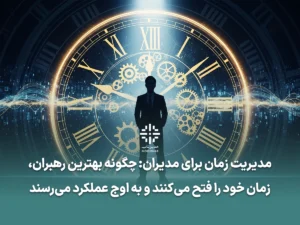
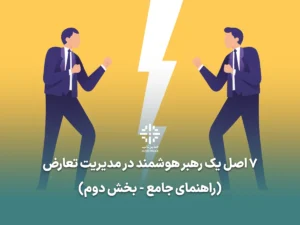
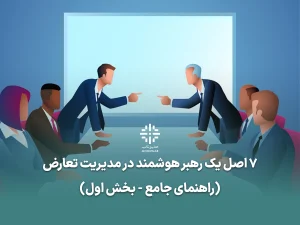
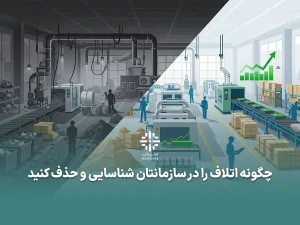
میانگین امتیاز 0 / 5. تعداد آرا: 0